Emma Lacey
Aims to transform the fashion industry with her mono-material approach to sustainable product design
We invited Emma Lacey, a recent graduate of Falmouth University's BA (Hons) Sustainable Product Design course to tell us about her graduate project, Mono. Here Emma shares the inspiration and drivers behind creating a jacket suitable for rock climbing that doesn’t harm the planet or humankind.
What is Mono?
Social sustainability has always been at the forefront of my designs and my Mono jacket is no exception. Completed in my final year studying Sustainable Product Design at Falmouth University, the project showcases the sustainable advantages of wool and challenges perceptions regarding the material’s capabilities.
Mono is a mono-material jacket, made from natural materials that were sourced locally within a 10-kilometre radius from where the product was constructed in the Lake District. The piece was created for use by rock climbers and therefore ease of movement was a key consideration during the design process. The wool is given engineered stretch at key articulation points through the innovative use of pleating. The result is a made-to-last jacket, which breathes and moves with the user; a jacket which does not harm the planet or humankind.
The inspiration behind the jacket
During the summer of 2019, I took part in a rock-climbing trip to the Langdale Valley. This experience - which combined a sport with which I am obsessed and an appreciation of our natural resources - was the shaping influence upon my final project.
Whilst in the Lake District, I would regularly visit local rock climbing shops and stare in awe at all the climbing gear. But soon this awe was replaced with concern as the majority of these products were constructed from a mismatch of synthetic materials welded and glued together. Such practices are becoming increasingly common within the manufacture of sports clothing. Manufacturers will justify increased use of synthetic mixtures due to a product's intended high usage. However, such products are increasingly entering the fast fashion systems, where they are becoming obsolete and outdated after a season - or less.
Acknowledging the need to design-out the problems surrounding lack of recycling and re-use at the end of a product’s life span, meant that I wanted to ensure that the project would focus on promoting mono-material usage. As a natural alternative to synthetics and a material that also happens to be found in abundance in the Lake District, wool was the perfect substitute.
An interesting characteristic of wool is that it can offer different properties, dependent on the variety of sheep chosen. As sheep have been bred over generations in different locations, their wool has adapted to the environment in which they are now found. In order for them to best survive, their wool becomes best-suited to that exact location. This is extremely useful when producing clothing in the location for which it is intended to be worn. These adaptations allow for the ability to hand pick wool, pre-adapted to a specific environment, without the use of any chemicals or need for synthetic materials.
“Currently, the majority of British wool will be sold at auction, meaning it is hard for the price per fleece to increase, or to ensure a strong financial return for the farmers.”
Sustainable advantages of British Wool
At the start of my project, I visited Liskeard’s Wool Sorting Depot and learnt that the return for a shorn fleece is staggeringly small. Currently, the majority of British wool will be sold at auction, meaning it is hard for the price per fleece to increase, or to ensure a strong financial return for the farmers.
This insight was a massive motivator for my project. Not only did I want to promote the usage of British wool, but I also hoped to practice a holistic design concept, based upon the triple bottom line: bringing together as one the local economy, the environment, and people. As fashion moves towards more ethical and sustainable material approaches, I believe it is crucial that we do not overlook the people making the products, or those who supply fabrics. In this project, these makers are the farmers. My goal with Mono was to allow these people (and their wool) the recognition and fair pay they deserve.
Manufacturing locally was one major sustainable advantage that came from utilising British wool and pushed me to ensure that other aspects of my design were equally sustainable. When designing the jacket I deliberately designed-out the need for zips and other fastenings, by instead utilising pleats for ease of use. This meant I no longer had to import materials for other parts of my jacket and ensured the jacket could be produced entirely within the Lake District from start to finish. I was, therefore, able to dramatically cut the carbon footprint of the jacket, transportation costs were lowered, and time spent making each jacket was decreased; the transparency and traceability became as open as possible.



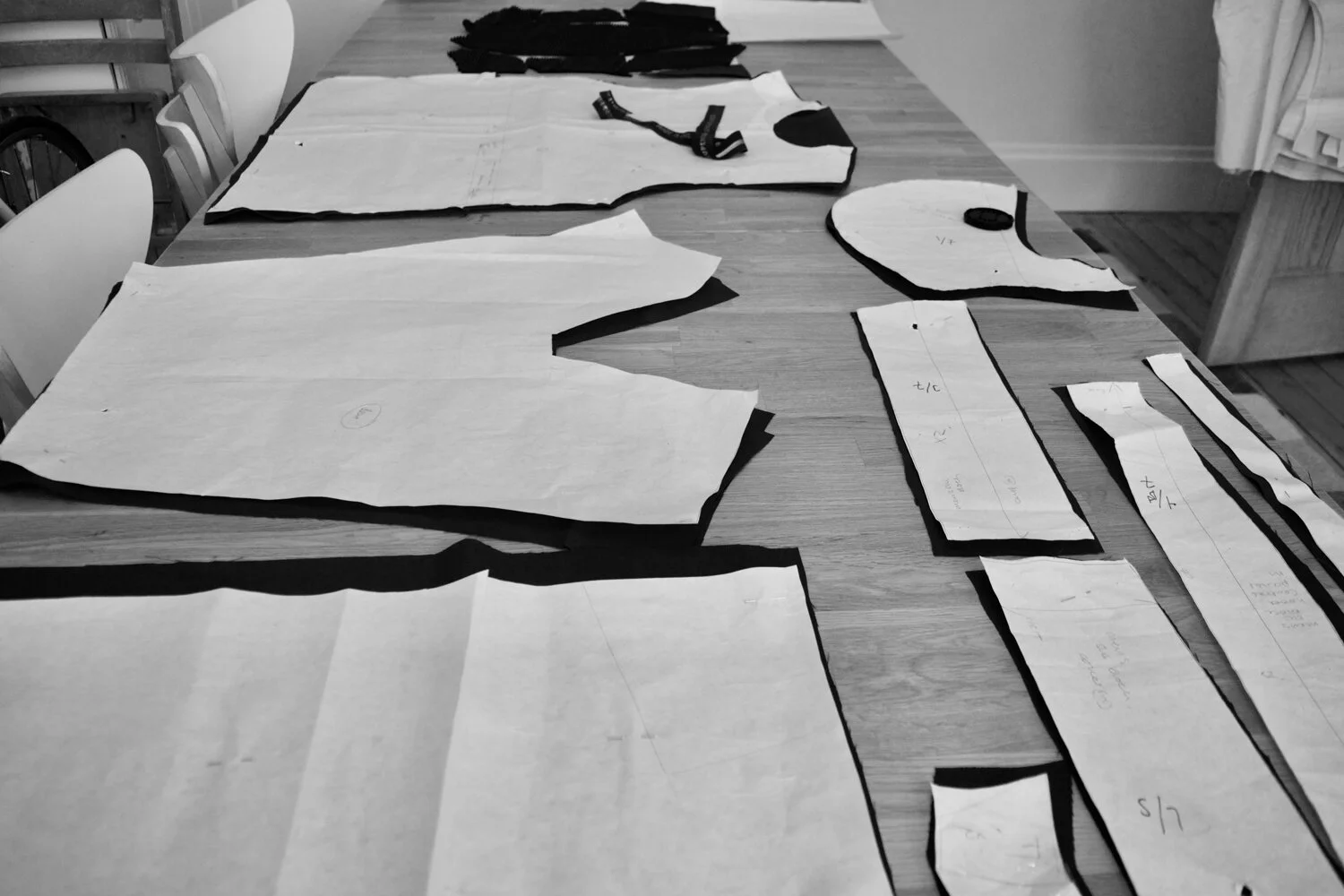


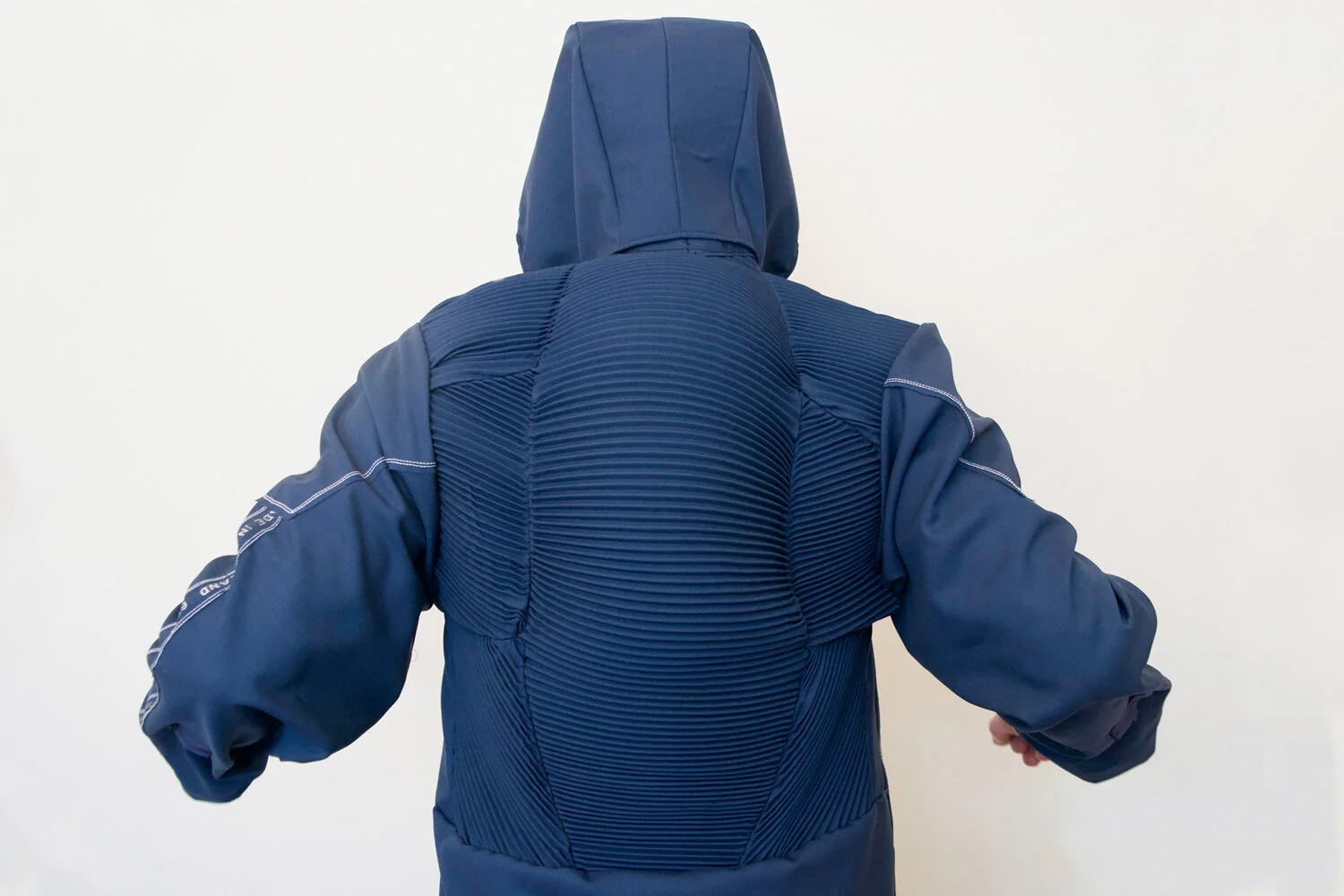
Behind the pleats
In order to produce the Mono jacket within the Lake District alone, I secured an internship with F.Ciment Pleating in London as a means to learn the pleating process. I could have had the pleats made for me and posted down to Cornwall, but so often the route of gaining knowledge is from afar, with no physical link. I strongly believe that having a hands-on approach with any project - seeing, and being part of the manufacturing process - allows for a much deeper understanding and knowledge. This gives a greater insight into what the capabilities are, and where the real innovation and potentials lie.
I am often asked exactly why pleats are so important within my design. The Mono jacket had to perform to the same level, if not out-do, a synthetic climbing jacket, in order to fully highlight the impressive capability of wool. However, one shortcoming of wool is its inability to stretch. Mapping the kinesiology of the back was therefore important in order to fully understand the movement and flexibility required of the jacket by the wearer. This gave me the inspiration to use pleating to combat the lack of stretch. The back of the jacket is therefore mapped against the sections of muscle with each area of pleat replicating their direction of movement.
Longevity
Longevity is a huge part of making a product sustainable. You might design the most attractive product but, if it doesn’t perform or last, it will inevitably come to its ‘end-of-product’ life much sooner, regardless of how sustainable the material is. It was therefore important to me that I was able to design a jacket that would genuinely improve a rock climber’s experience. Working with local rock climbers, we discussed what was thought to be missing from jackets currently on the market. These conversations suggested that reinforced sections on specific areas, such as those that rubbed against harnesses, was one feature in which normal jackets lacked - this was added as a key part of the design.
The challenges faced
As with all projects, the Mono jacket faced a few challenges along the way. For example, like all public spaces, my University was forced to shut due to the COVID-19 pandemic. I, therefore, moved back home for lockdown. During this time, I was grateful for the pressure of deadlines as it meant time passed quickly. The dining room table was extended and patterns hung on the door, with sewing machines and threads over spilling. My dad became a model and a makeshift backdrop was created.
What I missed (and still miss) is being able to bounce ideas around the studio. Collectively working together is so important, as so often the person sitting next to you will look at your work with a completely different viewpoint, and give you the constructive feedback you might need.
However, not everything was a challenge. The jacket was the first piece of clothing I have made, and by approaching the design process with a focus on creating something that would be genuinely useful, I believe it allowed for freedom during the process. I didn’t feel trapped by what is perceived to be the correct method of designing or making as this project was something that hadn’t been done before.
What’s next for me?
My time studying at Falmouth University has ensured that sustainability, innovation and human-centred design research will always be at the forefront of my work. Designing for social and sustainable good, with a focus on HCD research, is where I hope to pursue a career. I hope I get the chance to work on exciting new projects, where there lies the potential for real sustainable innovation.
I stay optimistic and try to look for the silver linings surrounding COVID-19. At the very least, the pandemic has showcased that if we want change, we have to act now. We can no longer simply wait and hope for the best; as a society, we must work collectively and join together. I hope this means that sustainability will be taken more seriously and that more companies, who have the power to make change, will begin championing sustainability at all levels.
Contact Emma via email or LinkedIn
All images copyright of Emma Lacey, Studio Lacey.
23.09.2020